Embracing Technological Innovation: The Imperative for 3PLs in the Modern Logistics Era
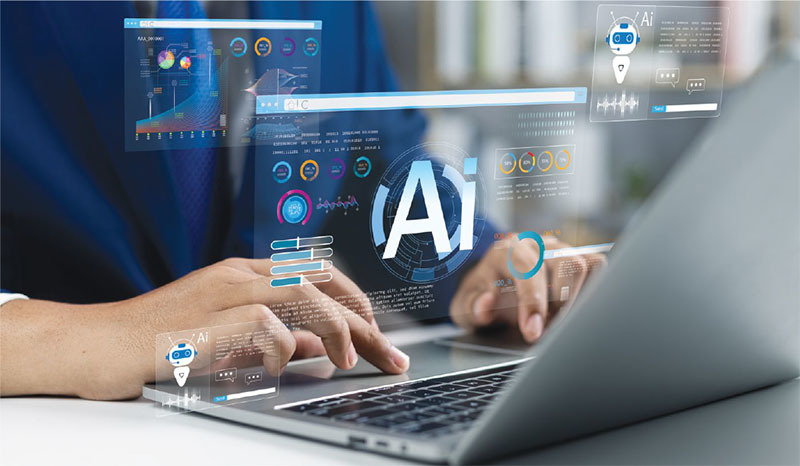
THE LOGISTICS INDUSTRY has reached a pivotal juncture where integrating technology is no longer just a competitive strategy but a fundamental requirement for logistics providers aiming to scale their operations. Sure, there are small boutique brokers still operating on a rolodex, and that very may well continue to work for them on a handful of accounts, however, embracing tech is all about scalability.
The surge in logistics demand post-COVID led to an explosive need for human capital, but soon after that came to an end and many organizations were forced to reduce their headcount at the whim of the cyclical nature of the trucking industry. This pattern not only affects the industry’s operational efficiency, but also its reputation and partner relationships.
We at Circle Logistics decided to set on a mission to break the effect of these cycles as much as possible by adopting technology that enables logistics providers to scale operations fluidly while maintaining a stable workforce. Over the last two years, there has been a committed effort to redefine growth strategies.
The two primary objectives included:
- Implementing scalable technology that can adapt to the fluctuating economic conditions of boom-and-bust cycles; and
- Empowering employees to transition from routine operational tasks to strategic roles.
An in-depth analysis within Circle Logistics pinpointed three areas where human effort was significantly tied up in repetitive tasks:
- Transactional Phone Calls — Managing calls for bookings, updates and service inquiries.
- Update Emails or Simple Data Exchange — Sending routine updates on load status or operational changes.
- Multiple Disparate Systems — Systems interconnected with our Transportation Management System (TMS) but lacking integration among themselves, necessitating manual oversight.
In response, we embarked on a transformative journey, focusing on:
- API-driven Workflow Triggers — To automate and synchronize data flow between systems.
- Artificial Intelligence (AI) — To revolutionize communication and operational decision-making.
- Robotic Process Automation (RPA) — To automate routine tasks, thereby freeing up personnel for more strategic roles.
Post-implementation, Circle Logistics has not only seen record highs in unit economics across various departments but also has fostered an environment where employees engage in more critical, thoughtful work.
Revolutionizing Communication with AI
In early 2024, we partnered with Pablo Palafox, CEO of Happy Robot, an AI startup, to pioneer AI-driven calls. After a brief but intensive training period on the specifics of freight brokerage, we launched this innovative solution in June. To date, we have conducted more than 200,000 calls, with a goal to handle up to 1 million in 2025.
This initiative reduced manual call handling by an impressive 80-100% across all scenarios, eliminated wait times and significantly boosted customer/carrier satisfaction and operational efficiency. Moreover, AI has ensured consistency in negotiation tactics and enhanced fraud detection.
Drawing from my more than 15 years in freight tech, partnerships often reveal unexpected challenges. However, our collaboration with Happy Robot was exceptional in yielding additional benefits, notably in data analytics. We’ve unlocked a wealth of data from our phone calls that provide deep insights into market trends, carrier efficiency and customer preferences, which were previously inaccessible at this scale.
Operational Efficiency through RPA
The strategic application of RPA has not only saved numerous manhours but also has positively transformed the work culture. By automating tasks like spot quote processing and load status updates, RPA has streamlined operations, allowing our staff to shift focus towards strategic planning, which has led to increased efficiency, employee satisfaction and retention in an industry notorious for high staff turnover.
API Driven Workflow Triggers
Our quest for technological efficiency revealed a gap in our system integrations; while we had more than 20 integrations in our TMS, they functioned in isolation. Through strategic partnerships with Transport Pro and extensive stakeholder collaboration, we developed automated workflows.
For example, receiving a tracking update now automatically triggers multiple actions: a text to the driver, an email to the receiver and an EDI update to the customer, all without human intervention.
In today’s fast-paced world where speed and precision reign supreme, technology indeed provides a competitive edge. By automating our workflows, we’ve shifted our focus from routine checks to exception management, enabling our team to leverage data for strategic decision-making.
A Case for Minimal Financial Investment
Remarkably, these advancements at Circle Logistics were accomplished with a relatively modest investment compared to our competitors. This case exemplifies that transformative technology isn’t always about large financial outlays but about foresight, strategic alliances and effective execution.
Investing in technology yields significant long-term benefits through the reduction of manual labor, enhancement of process accuracy and improvement in operational reliability. Automation liberates staff from mundane tasks, allowing them to engage in activities that add more value, like building relationships and thinking innovatively.
Setting New Industry Standards
By pioneering technological innovation, Circle Logistics isn’t merely enhancing its own performance but is also setting new industry benchmarks. This leadership role prompts other 3PLs to reconsider their approaches, fostering an industry-wide culture of continuous improvement.
The adoption of technology in logistics transcends mere cost-saving or efficiency; it’s about redefining the core of how logistics functions. It’s about envisioning a future where logistics doesn’t just facilitate the movement of goods but propels forward with innovation and sustainability, and quality of life improvement for those who serve the logistics industry.
Smith, senior vice president of Circle Logistics in Chicago, is the TIA 2024 Technovator of the Year award winner. To learn more about how Circle embraces technology, email Smith at asmith@circledelivers.com.